Home / Corrosion Control Engineering / Cathodic Protection
Cathodic Protection
With forty years of experience in the corrosion control industry, Allied Corrosion is a leader in cathodic protection and leverages its know-how and expertise to ensure that your pipeline is cathodically protected according to latest NACE guidelines and “Recommended Practices”.
Cathodic Protection Design
The Allied Corrosion Difference
Risk Mitigation & Analysis
Compliance & Excellence
Cathodic Protection Services
- Cathodic Protection Installation
- Deepwell Cathodic Protection
- Linear Distributed Cathodic Protection
- Remote Distributed Cathodic Protection
- AC Mitigation
Cathodic Protection Applications
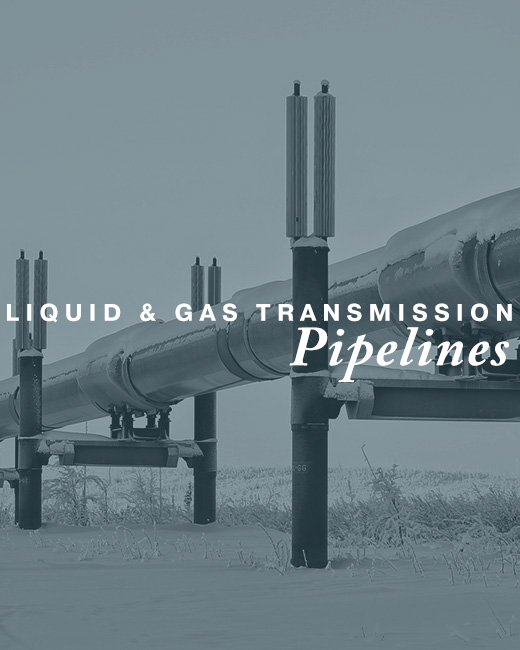
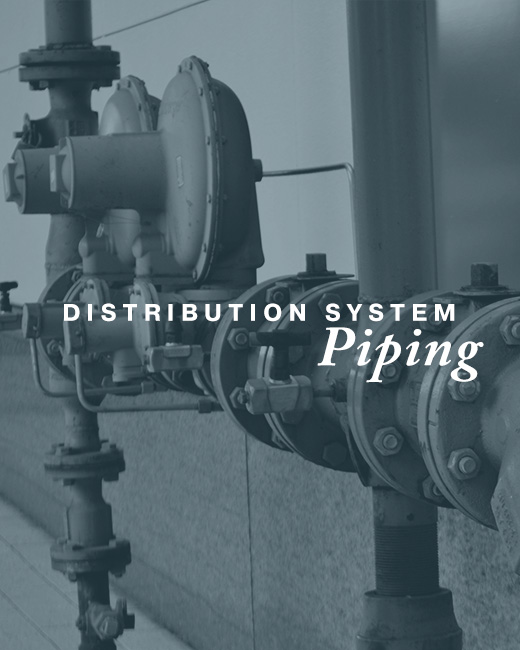
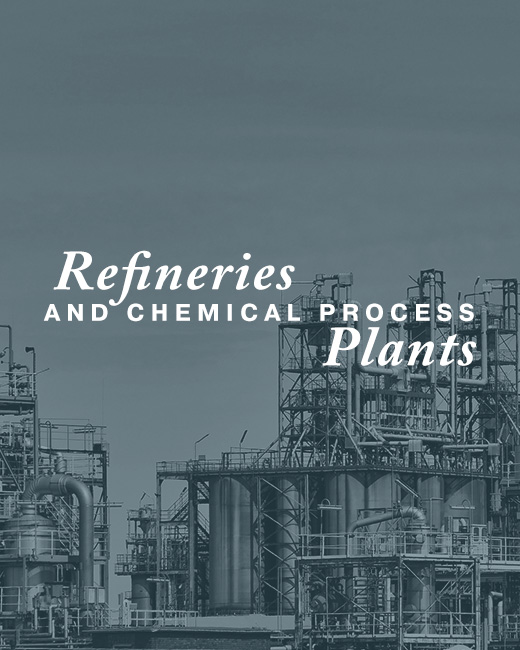
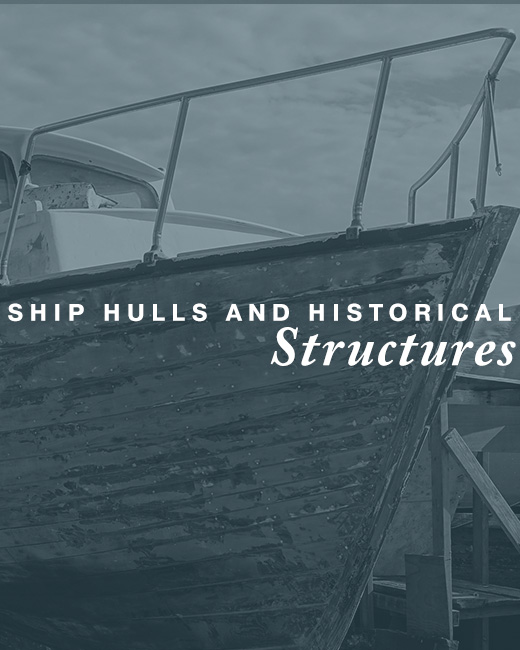
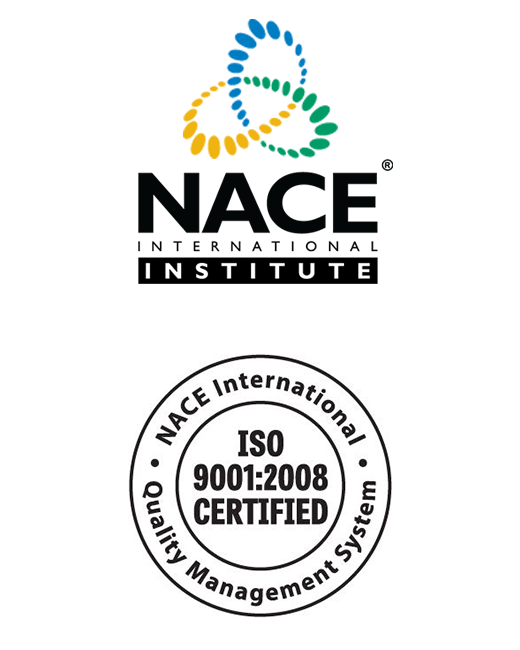
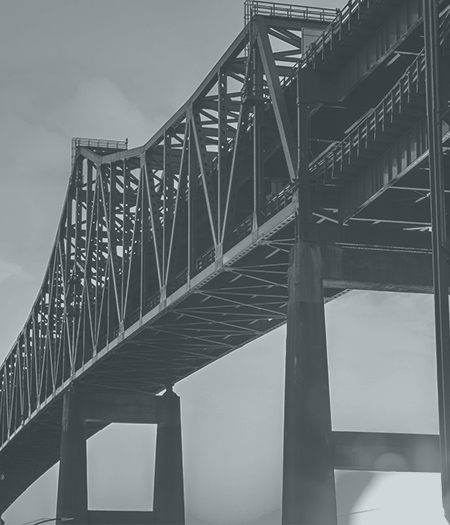
Cathodic Protection System Installation
Deep Well Cathodic Protection Systems
Deep Well Anode System installations are commonly used on transmission and distribution pipelines throughout the world. They can be installed on existing pipeline right-of-way, eliminating the additional cost of purchasing an easement for the cathodic protection system. In addition to the small area for installation, Deep Well Anode Systems tend to be the most efficient and economical means to achieving the Cathodic Protection criteria established in NACE SP-169-2007.
Quick Facts
- Deep Well Cathodic Protection Systems often can achieve a circuit resistance of 1 ohm or less.
- Anodes are placed in a column of coke backfill, which allows the current to discharge and travel up and down the entire coke column, allowing the entire coke column to be energized. This is often referred to as the active area the CP system.
- Quality and design of the coke column backfill are essential to the lifespan of a deep well cathodic protection system.
A typical Deep Well Anode System consists of drilling a 10 inch diameter hole between 200 and 900 feet deep. The depth is determined by the geological formations found in the area of the installation. Once the hole is completed, an electrical resistance log is recorded from the bottom to the top of the hole. Anode locations are determined using this log. Anodes are then lowered into the hole normally strapped to a stand/vent pipe.
Once the anodes are in place, calcined petroleum coke backfill, LORESCO Impressed Current Backfills, is fluidized and pumped from the bottom of the hole to a level above the top anode. This backfill is allowed to settle overnight and then it is checked to insure that the top anode is covered. Additional coke will be installed if necessary and the remaining hole filled with a hole plug/seal, LORESCO PermaPlug.
Typical anode materials include:
- Mixed-Metal Oxide Tubular Anodes
- High Silicon-Iron Anodes
- Threaded Graphite Anodes
- Platinum Wire Anodes
DC power supply units include standard cathodic protection rectifiers, DC Solar Panel Units, Natural Gas DC Generators, and Thermo-Electric Generators. Our engineering staff welcomes all opportunities to assist our customers with their deepwell CP design. This would include written cathodic protection specifications, actual turnkey installation, and system initialization and maintenance.
Linear Distributed Cathodic Protection Systems
Linear distributed anode systems are placed approximately five feet to the side and parallel to the pipeline which is to be protected. Linear distributed anode systems are specifically used primarily where there is a lot of other buried utilities nearby the pipeline which is to be protected. Generally the current output of the linear distributed anode system is low, but consistent and continuous along the entire length of the anode system.
Quick Facts
- Deep Well Cathodic Protection Systems often can achieve a circuit resistance of 1 ohm or less.
- Anodes are placed in a column of coke backfill, which allows the current to discharge and travel up and down the entire coke column, allowing the entire coke column to be energized. This is often referred to as the active area the CP system.
- Quality and design of the coke column backfill are essential to the lifespan of a deep well cathodic protection system.
A typical Deep Well Anode System consists of drilling a 10 inch diameter hole between 200 and 900 feet deep. The depth is determined by the geological formations found in the area of the installation. Once the hole is completed, an electrical resistance log is recorded from the bottom to the top of the hole. Anode locations are determined using this log. Anodes are then lowered into the hole normally strapped to a stand/vent pipe.
Once the anodes are in place, calcined petroleum coke backfill, LORESCO Impressed Current Backfills, is fluidized and pumped from the bottom of the hole to a level above the top anode. This backfill is allowed to settle overnight and then it is checked to insure that the top anode is covered. Additional coke will be installed if necessary and the remaining hole filled with a hole plug/seal, LORESCO PermaPlug.
Typical anode materials include:
- Mixed-Metal Oxide Tubular Anodes
- High Silicon-Iron Anodes
- Threaded Graphite Anodes
- Platinum Wire Anodes
DC power supply units include standard cathodic protection rectifiers, DC Solar Panel Units, Natural Gas DC Generators, and Thermo-Electric Generators. Our engineering staff welcomes all opportunities to assist our customers with their deepwell CP design. This would include written cathodic protection specifications, actual turnkey installation, and system initialization and maintenance.
Remote Conventional Cathodic Protection Systems
Remote Conventional Cathodic Protection Systems are a more affordable option to deep well cathodic protection systems. This is based on the availability of inexpensive surface land being available because the anode array extends out form the rectifier a minimum of 200 feet on one side of the pipeline. In this kind of CP system the anodes are extended out perpendicularly from the pipeline.
Quick Facts
- Remote Conventional Cathodic Protection Systems are an alternative to Deep Well CP Systems when sufficient land is available.
- Remote Conventional Cathodic Protection Systems are more affordable than Deep Well CP Systems. This is based on the fact that conventional anode system have a typical anode depth of 20 feet, while the deep well anode system have a typical anode depth of 300+ feet.
When surface land is available, the remote conventional cathodic protection system may be a more economical alternative to the more expensive deepwell system. The typical installation will generally specify that the anodes be installed in a straight line and perpendicular to the pipeline. The first anode closest to the pipeline will typically be approximately 200 feet or more away from the pipeline. The anodes are then spaced approximately 20 feet apart and installed to a typical depth of 20 feet. Our engineering staff can assist with this type of installation when the physical conditions warrant it.
AC Mitigation
Quick Facts
- AC Interference can cause personal safety hazards on job sites.
- AC Mitigation can be accomplished through the installation of grounding rods, decouplers and linear grounding systems, such as zinc ribbon anodes or bare stranded copper cable.
- AC Mitigation needs to be considered in addition to cathodic protection where a pipeline is in or crosses a HVAC corridor.
We have assisted many pipeline owner/operators with their AC mitigation problems by finding low cost and long life solutions. Typically induced AC scenarios fall into two major categories. First is the “Step Potential” category. This exists when there is induced AC present on a pipeline appurtenance that can be touched by someone. When the induced AC exceeds 15 VAC, which is the safe “hand let-go” threshold for a normal size male, there is the danger of personal injury and/or death, and the problem should be mitigated. The second category is associated with pipeline segments where AC current is discharged from the pipe’s metal surface to the ground.
The two most common types of AC current discharge are steady state and fault current discharge. AC corrosion/metal loss will begin to occur whenever the threshold current density of 20 A/M2 is exceeded. The severity of metal loss for either type of discharge is directly related to the AC current density in the discharge area, and the discharge length of time. In some cases, actual pipe wall penetration/failure can result from just one massive ground fault event. We have been very successful in providing a variety of reasonable, well engineered AC Mitigation Systems for the pipeline industry.
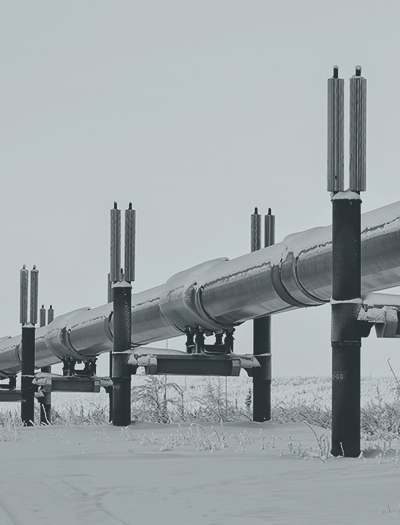
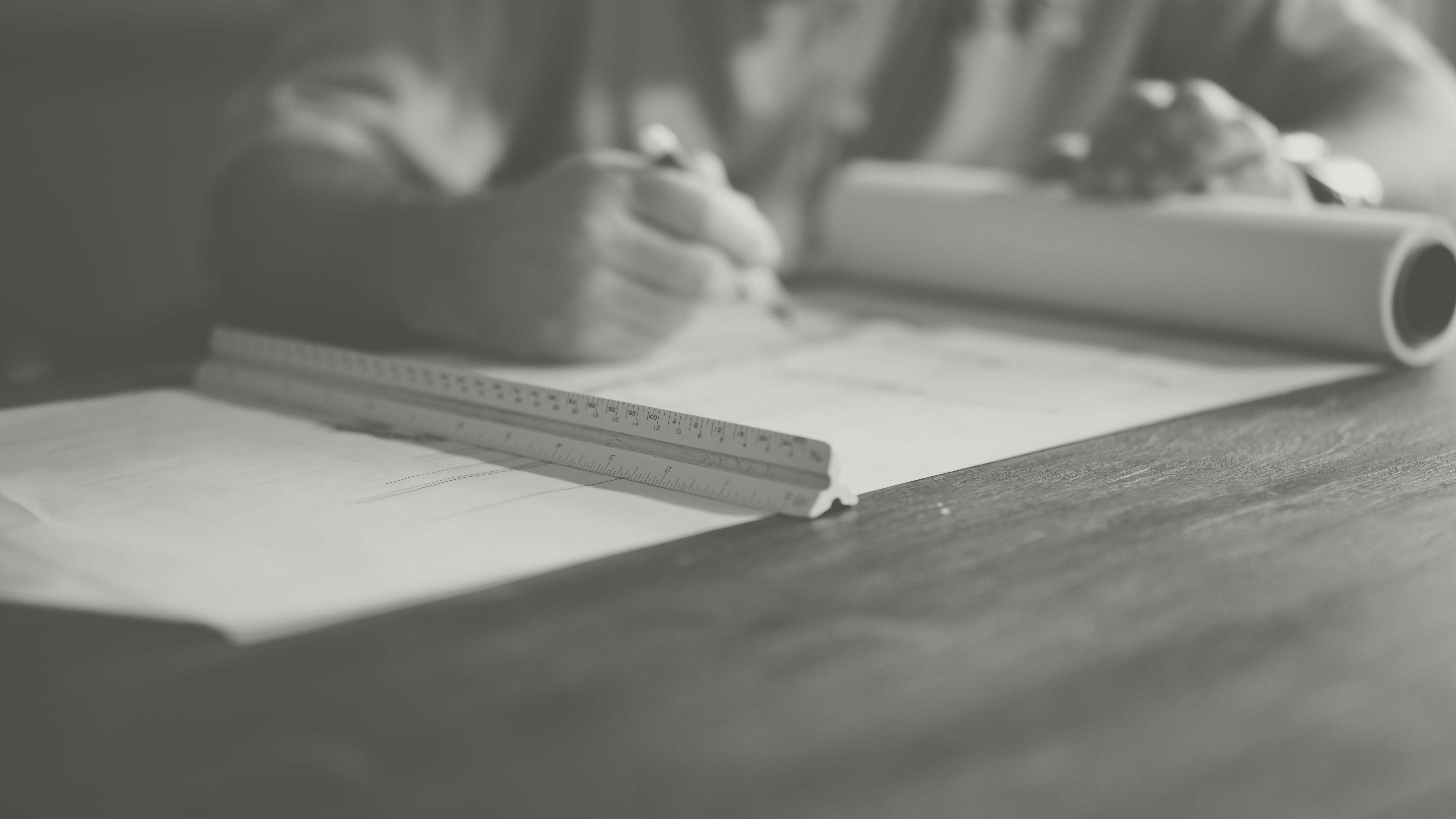
Contact Allied Corrosion Today
1550 Cobb Industrial Dr. | P.O. Box 9098 | Marietta, GA 30065-2098
770-425-1355 (Phone) | 770-425-1354 (Fax) | info@alliedcorrosion.com (Email)
©2018 Allied Corrosion. All rights Reserved.
Made with ❤ by Mighty Good Marketing