Direct Current Voltage Gradient Survey (DCVG)
What is DCVG?
Direct Current Voltage Gradient surveys are used to evaluate defects in pipeline coatings. Corrosion normally occurs where the bare metal surface of a pipeline comes in contact with its surrounding electrolyte (water and soil). The primary purpose of a DCVG survey is to find and size pipeline coating anomalies associated with corrosion.
DCVG equipment & procedures:
We use the PCS-2000 instrumentation when performing these surveys. This equipment uses time tested and field proven analog technology, enabling our crews to locate anomalies that other equipment uses time tested and field proven analog technology, enabling our crews to locate anomalies that other equipment may miss. All DCVG indications are electronically recorded with sub-meter accurate GPS location data using the Trimble GEO-HR GPS / Data Logger.
DCVG applications:
- One of the indirect inspection tools approved in ANSI/NACE standard RPO502-2002, Pipeline External Corrosion Direct Assessment (ECDA) Methodology.
- Verification of original coating condition on newly installed pipelines. The data collected can identify areas of potential coating concerns allowing the owner to make informed decisions on corrective actions.
- One of the indirect inspection tools approved in ANSI/NACE standard RPO204-2004, Stress Corrosion Cracking (SCC)Direct Assessment Methodology.
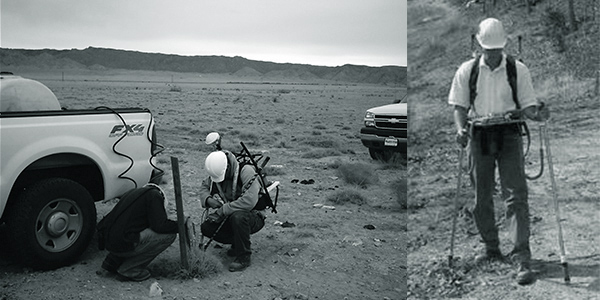
Find out about our other Field Services